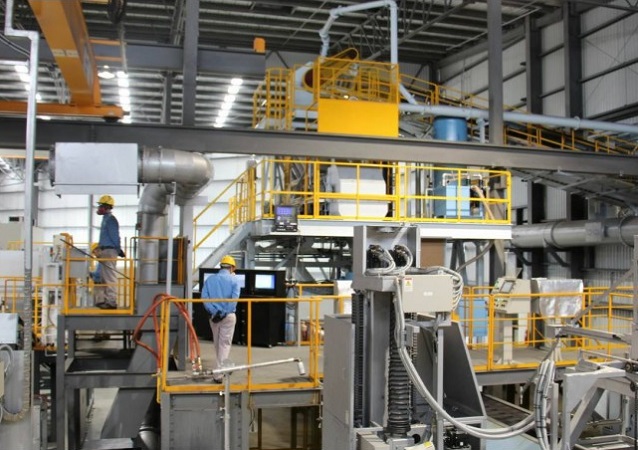
Honesty and courage Honesty and courage earn our greatest respect. Kitagawa has four key values to ensure best business practice. Lastly, Kitagawa’s industrial machinery division supplies tower cranes for building construction, concrete mixing plants and multi-story car parking.
Shaping the world.
Investment casting is a precision casting method which is growing steadily in international significance for reason of economy. The method is being used to produce larger and larger castings. Investment castings is also employed kitagawa investment casting an increasing scale for so-called super alloys which require ever more complex smelting processes. Due to the economic benefits it offers, increasing weight is being attached to investment kitagswa in comparative value analyses. Its scope for optimum shaping is unmatched by any other casting method. Investment castings-oriented design frequently offers an answer to technical problems which would be either impossible or far more expensive to implement using any other method. Generally speaking, the investment casting technique is used for small piece weights of between 1 g and 10 kg.
Japan-based Kitagawa Iron Works doubles die casting capacity in Aguascalientes
GitHub is home to over 40 million developers working together to host and review code, manage projects, and build software together. If nothing happens, download GitHub Desktop and try again. If nothing happens, download Xcode and try again. If nothing happens, download the GitHub extension for Visual Studio and try again. Three years ago I set out to build a foundry for producing high-detail aluminum casts using the investment casting process. The original model is cast four times two positives and two negatives , with the final positive cast out of the chosen alloy.
The Investment Casting Process
GitHub is home to over 40 million developers working together to host and review code, manage projects, and build software. If nothing happens, download GitHub Desktop and try. If nothing happens, download Xcode and try.
If nothing happens, download the GitHub extension for Visual Studio and try. Three years ago I set out to build a foundry for producing high-detail aluminum casts using the investment casting castibg. The original model is cast four times two positives and kitagawa investment casting negativeswith the final positive cast out of the chosen alloy.
See the budget presets at the end of this article for a complete list of all tools mentioned. With investment casting you can reproduce every detail of the master model, such as polished surfaces and sharp features. The only finishing required is cutting off sprues and restoring lost detail in places where the sprues used to connect. This only matters when they are combined with other parts produced through a different method — otherwise they fit into each other like the master models.
To cxsting a rubber mold, build a wooden or plastic box slightly larger than the model, fix the model in the box, and pour rubber over it. If you keep the box walls as separate components, you can quickly build boxes of any pre-determined size. If you simply cut the master model out of the mold with an X-Acto knife you will produce a one-part mold, but releasing a fragile wax pattern cast from this mold could be next to impossible without breaking it.
For this reason, complex models require two-part molds. You can also create additional geometry at this stage to aid degassing or to add strength to the wax pattern cast from cwsting mold:. Entrapped gas is a concern with rubber molds as any bubbles held at the surface of the model by surface tension will become filled spheres on a cast positive. To prevent this, spray the model with a mold release compound before pouring the rubber.
Degass the rubber before pouring by placing the container in a vacuum chamber until full vacuum is reached and the rubber «boils over».
Select a pattern wax based on mechanical strength and expansion ratio, which are directly related. With «machinable» wax every mold can be a simple one-part mold because the casts are less likely to break when pulled out of the mold. On the other hand, investment will be cracked by expanding wax during flash-firing or autoclaving if the wax has a high enough expansion ratio. The tools and process required to cast wax patterns from rubber molds depend on the size of the parts:.
After you «chase» the wax pattern by removing any vents and supports with a wax pen, attach it to a rubber base using sprues. When you invest the flask later, the rubber base will give the top of the flask a funnel shape for pouring metal. You can sprue patterns faster by using bulk-extruded wax sprues and breaking off pieces of any required length. Connecting sprues to the rubber base and the model with «sticky wax» will also reduce re-work invesgment form stronger connections.
A poorly attached wax pattern will break off the base and float to the surface as the flask is being invested. Use fewer sprues and place them at strategic points «gates» following thin sections, which will give the metal alternate pathways for filling the mold before solidifying.
Placing too many gates in close proximity will cause turbulence from several streams of molten metal colliding under pressure and wasting energy otherwise used to fill mold details, which will result in incomplete fills. Turbulence can also break off small internal features of the mold and they will end up being embedded in the kitagawa investment casting as «inclusions». Select your investment based on the metal alloy ferrous or non-ferrous and extra features like less dust while mixing.
Investment powder is castign by weight in boxes or drums, and mixed with deionized water based on a ratio castinf by the manufacturer. I prefer UltraVest for aluminum casting. Deionize the water before mixing it with investment to filter out knvestment particles that weaken the mold. Portable deionizers are easy to get because they are also used for washing cars.
I prefer using rubber bowls for mixing; plastic containers become consumables, requiring continuous replacement. Calculate the volume of investment required to fill the flask an inch above the model. Then, consult the table provided by the manufacturer to determine the weight of investment and water required for mixing. When several mix ratios are available, start in the middle and then select a ratio resulting in the strongest mold more investment while providing enough working time more water.
Fill one rubber bowl with water and another one with investment, using a digital scale for weighing. Then, sift the investment into the water with a whisk. Blend any clumps quickly, leaving enough time to vacuum and pour the investment.
If the mixture thickens before the process is complete it will not fill the whole flask. Large amounts of investment set faster than small amounts. Degass the liquid investment in a vacuum chamber twice while vibrating it with an oscillator: first kitagaws mixing and then after pouring into the flask. The vacuum chamber and pump must be well maintained to reach full vacuum before the investment starts thickening. If the investment molds still have bubbles after innvestment, spray a layer of anti-sticking compound on the wax patterns before investing.
One example is Rio VacuFilm, which can be mixed into a gallon of methyl alcohol using a gradated beaker. You can wind the rest of the flask with the same tape, or purchase a sleeve kitzgawa with the flask and use it to immediately cover the whole flask. Pour investment into the flask at an angle to avoid creating more bubbles and use a funnel to reduce spillage.
Store castinb a dry, vibration free area after kitagwa last degassing. Lastly, scrape the flask with a fettling knife to remove any investment overhangs that could cause it to get stuck in the vacuum-assist chamber. Following autoclaving or flash-firing, burn out the molds in a kiln using the schedule provided by the investment supplier in order to evacuate water and fuse fibers in the micro-structure of the mold. Molds with intricate details require a longer burnout to achieve higher strength.
Large molds require more time due to the amount of material to undergo transformation. A manual kiln requires constant and close monitoring as catsing result in cracked molds. Programmable kilns are expensive because they are marketed to dentists and jewelers, but they save time and increase quality.
Another option popular with makers is adding thermocouples and a controller to a used manual kiln. Running a kiln requires a metal desk, a room with a stone floor, all non-ceramic surfaces covered with sheet rock, corners sealed with fire foam, and a ventilation. Large kilns run on V and require converting a V circuit, installing fuses, and routing through a fusible safety switch. These changes should be included in budget and feasibility analysis. Transfer autoclaved molds directly into a pre-heated kiln to avoid cracking from rapid cool-down.
When using flash-firing the burnout can start immediately in the same kiln. Use an alloy designed for casting rather than machining, for example instead of Your goal when casting is to transfer the flask from the kiln to the vacuum assist chamber and pour metal in 2 minutes or. This avoids a thermal shock that can destroy intricate mold details as the flask rapidly cools to room temperature, causing them to break off and become embedded in the casting.
Position the vacuum-assist chamber close the burnout kiln so that the flasks can be transferred quickly. Take the crucible out of the forge and place it nearby before opening the kiln to remove a flask. Use a thermocouple probe for taking measurements. Once the metal in the crucible reaches the casting temperature, transfer the flask into the vacuum-assist chamber with a running vacuum pump. Use a temperature resistant O-ring to seal the flask flange to the top of the chamber.
This will generate vacuum around the outside of the flask, drawing gases inside the flask out through the walls. While the small gas cxsting can permeate the mold due to its porous microstructure, the metal. Castijg the metal will be pulled toward the walls of the mold, precisely capturing surface details. If the vacuum is not enough to achieve a complete fill, you can attach a «riser» to the top of the flask to increase the weight of metal pushing down into the mold.
Risers also let you pour quickly and avoid dangerous spills because they buffer the metal and feed it at a slower rate while keeping it hot.
Install a ceramic filter inside the riser to prevent kitafawa of forge refractory, dust, and other unwanted particles from entering the mold and becoming inclusions. Finally, tilt the crucible with a shank to pour metal into the flask. I will cover running the forge and building the vacuum-assist chamber in future articles. The vacuum-assist chamber is simply a do-it-yourself version of a vacuum casting machine pioneered by Neutec. Wait a total of 20 minutes after the pour before quenching the flask in a bucket filled with water.
You can remove the flask from the vacuum-assist chamber when the portion of metal visible from the outside solidifies. The top of the flask will blow out a chunk innvestment investment on contact with water. Use a fettling knife to increase the size of the resulting hole, scooping investment out of the flask while dipping it in water. You can grab the cast by the sprue with pliers and wiggle it investmeent of the flask, making it easier to scoop out remaining investment.
Used investment can be stored in the same bucket or in a thick plastic bag until it’s taken to the dump. You can use metal files, sanding wheel, and sand paper to finish cast pieces after you snip sprues with a sprue cutter. For intricate detailing, try using a flex shaft tool. In this section I list all tools and consumables mentioned throughout the article with a few budget presets for. You can build any of these tools yourself to save on the cost, if you are willing to spend the time.
Skip to content. Dismiss Join GitHub today GitHub is home to over 40 million developers working together to host and review code, manage projects, and build software. Sign up. Investment Casting for Makers. Branch: master New pull request. Find file.
Download ZIP. Sign in Sign up. Go .
Investment casting Wax assembly clean up
Day Range. Kitagawa has four key values to ensure best business practice. Kodama Chemical Industry Co. Kitagawa has built a reliable reputation by consistently providing exceptional technology across a variety of manufacturing industries. Cycle Time While investment casting and die casting both produce complex parts, the cycle times differ greatly. Machine tool accessories A leader in the global supply of Power chucks for turning centres and Kitagawa investment casting rotary tables for vertical machining centres and other machine tool accessories. No Recent Tickers Visit a quote page and your recently viewed tickers will be displayed. Search Tickers. All rights reserved Last updated Kogi Corp. If you are casting only a few parts or require larger size or stainless steel, investment casting may be the lower cost option. Another of Kitagawa’s divisions supplies Power Chucks and NC Rotary tables among other accessories to the global machine tool industry. This integral production requirement demonstrates Kitagawa’s vast experience in improving and maximising the effectiveness and efficiency of work holding products for the automotive industry. However, if you are looking to use stainless steels or copper alloys, investment casting is the better option. Lastly, Kitagawa’s industrial machinery division supplies tower cranes for building construction, concrete mixing plants and multi-story car parking. Cluster Technology Co. Last Updated: Dec 27, p.
Comments
Post a Comment