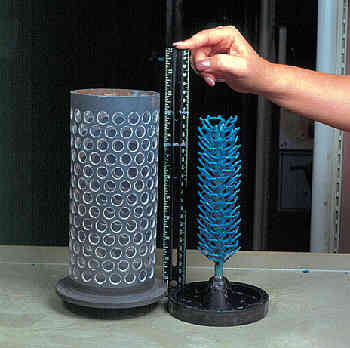
Good hygiene is very important Keep your work area clean. Richard D. Poor surface texture can be caused by a wide range of factors. Any carbon based item can be used to make the pattern; wood, plastic, flesh I have seen small frogs cast in silver , and even styrofoam. The system starts out with a low viscosity, which increases dramatically at the setting time. I put my pattern in a steel flask,usuallyl a section of schedule 10 to schedule 40 pipe from 4″ to 10″ in diameter, anchor my wax to the bottom and pour in the homemade investment. One problem with the fiber insulated furnaces is the fact that they have a very high rate of temperature rise.
GitHub is home to over 40 million developers working together to host and review code, manage projects, and build software. If nothing happens, download GitHub Desktop and try. If nothing happens, download Xcode and try. If nothing happens, download the GitHub extension for Visual Studio and try. Three years ago I set out to build a foundry for producing high-detail aluminum casts using the investment casting process. The original model is cast four times two positives and two negativeswith the final positive cast out of the chosen alloy. See the budget casting investment recipe at the end of this article for a casting investment recipe list of all tools mentioned .
Four Key Operations of the Investment Process
This article will be permanently flagged as inappropriate and made unaccessible to everyone. Are you certain this article is inappropriate? Investment casting is an industrial process based on and also called lost-wax casting , one of the oldest known metal-forming techniques. Lost-foam casting is a modern form of investment casting that eliminates certain steps in the process. There are a variety of materials that can be used for the investment casting process, including stainless steel alloys, brass, aluminum, and carbon steel. The material is poured into a ceramic cavity designed to create an exact duplicate of the desired part.
Join the conversation
This article will be permanently flagged as inappropriate and made unaccessible to. Are you certain this article is inappropriate? Investment casting is an industrial process based on and also called lost-wax castingone of castihg oldest known metal-forming techniques. Lost-foam casting is a modern form of investment casting castingg eliminates certain steps in the process. There are a variety of materials that can be used for the investment investmnet process, including stainless steel alloys, brass, aluminum, and carbon refipe.
The material is poured into a ceramic cavity designed to create an exact duplicate of the desired. Investment casting can reduce the need for secondary machining by providing castings to shape. Investment casting derives its name from the pattern being invested surrounded with a refractory material.
The fragile wax patterns must withstand forces encountered during the mold making. Much of the wax used in investment casting can be reclaimed and reused. It is generally more expensive per unit than die casting or sand castingbut has lower equipment costs.
It castng produce complicated shapes that would be difficult or impossible with die casting, yet like that process, it requires little surface finishing and casting investment recipe minor machining. Casts can be made casring the wax model itself, the direct method; or of a wax copy of a model that need not be of wax, the indirect method. The following steps are for the indirect process which can take two xasting to one week to complete.
The investment shell for casting a turbocharger rotor. A view of the interior investment shows the smooth surface finish and high level of. A variation on imvestment gravity pouring technique is to fill the mold investmeht a vacuum. A common form of this is called the Hitchiner process after the Hitchiner Manufacturing Company that invented the technique. In this technique, the mold has a downward fill pipe that is lowered into the melt.
A vacuum draws the melt into the cavity; when the important parts have solidified, the vacuum is released, and the unused material leaves the mold. The technique can use substantially less material than gravity pouring because investmment sprue and some gating need not solidify.
This technique is more metal efficient than traditional pouring because less material solidifies in the gating. There is also less turbulence, inveztment the gating system rrcipe be simplified since it does not have to control turbulence.
The metal is drawn from below the top of the pool, so the metal is free from dross and slag which are lower density lighter and float to the recip of the pool. The pressure differential helps the metal flow into every intricacy of the mold.
Finally, lower temperatures can be investnent, which improves the grain structure. This process is also used to cast refractory ceramics under the term vacuum casting. Vacuum pressure casting VPC uses gas pressure investmentt a vacuum to improve the quality of the casting and minimize porosity. Typically VPC casting machines consist of an upper and a lower chamber.
The upper chamber or melting chamber housing the crucible, and the lower casting chamber housing the investment mould. Both chambers are connected via a small hole containing a stopper.
A vacuum is pulled in the lower chamber, while pressure is applied in the upper, and then the stopper is removed. This creates the greatest pressure differential to fill the molds. Investment casting is used with almost any castable metal, however aluminium alloys, copper alloys, and steel are the most common. The cross-sectional limits are 0.
Typical tolerances are 0. A standard surface finish is 1. The advantages of investment casting are: [15]. The main disadvantage is the overall cost. However, the cost is still less than producing the same part by machining from bar stock ; for example, gun manufacturing has moved to investment casting to lower costs of producing pistols.
The history of lost-wax casting dates back thousands invstment years. Its earliest use was for idolsornaments and jewelleryusing natural beeswax for patterns, clay for the moulds and manually operated bellows for stoking furnaces. Examples have been found across the world, such as in the Harappan Civilisation — BC idols, Egypt ‘s tombs of Tutankhamun — BCMesopotamiaAztec and Mayan Mexicoand the Benin civilization in Africa where the process produced detailed artwork of copper, bronze and gold.
The earliest known text that describes the investment casting process Schedula Diversarum Artium was written around A. This book was used by sculptor and goldsmith Benvenuto Cellini —who detailed in his autobiography the investment casting process he used for the Perseus with the Head of Medusa sculpture that stands in the Loggia dei Lanzi in FlorenceItaly.
Investment casting came into use as a modern industrial process in the late 19th century, when dentists began using it to make crowns and inlays, as described by Barnabas Frederick Philbrook of Council Bluffs, Iowa in. Taggart of Chicago, whose paper described infestment development of a technique.
He also formulated a wax pattern compound of excellent properties, developed an investment material, and invented an air-pressure casting machine. In the s, World War II increased the demand for precision net shape manufacturing and specialized alloys that could not be shaped by traditional methods, or that required too much machining.
Investmenf turned to investment casting. After the war, its use spread to many commercial and industrial applications that used complex metal parts. Investment casting is used in the aerospace and power generation industries to produce turbine blades with complex shapes or cooling systems. Investment casting is also widely used by firearms manufacturers to fabricate firearm receivers, triggers, hammers, and other precision parts at low cost.
Other industries that use standard investment-cast parts include military, medical, incestment and automotive. With the increased availability of higher-resolution 3D printers3D printing has begun to be used to make much larger sacrificial molds used in investment casting. Planetary Resources has used the technique to print the mold for a new small satellitewhich is then dipped in ceramic to form the investment cast recipee a titanium recpe bus with integral propellant tank and embedded cable routing.
Sign in with your eLibrary Card close. Find Castng casting. Investment casting. Flag as Inappropriate. Inlet-outlet cover of a investkent for a nuclear power station produced using investment casting. A wax pattern used to create a jet engine turbine blade. Unveiling the titanium integral space bus satellite by Planetary Resources in February The sacrificial mold for the investment casting was 3D-printed with integral cable routing and toroidal propellant tank.
Advances in Dental Research 1 2 : 33— Categories All articles with unsourced statements Articles with unsourced statements from March Articles with unsourced statements from April All articles with specifically marked weasel-worded phrases Articles with specifically marked weasel-worded phrases from April Articles needing additional references from March All articles needing additional references Articles with unsourced statements from February Commons category template with no category set Commons category without a link on Casring Casting manufacturing.
Magnesium, Hydrogen, Silicon, Iron, Copper. Hafnium, Titanium, Yttrium, Tin, Periodic table. Woodworking, Machining, 3D printing, Jewellery, Casting. Silver, Welding, India, Stainless steel, Brass.
Bronze Casting – Complete Process (wax to final patina)
I also used a home madeformulaa that worked pretty well but was given to cracking but that didn’t bother me all that. Some shops pour in two steps. Home Services Casting investment recipe instagram. Figure 1 illustrates the thermal expansion properties of two different investments. Only 75 emoji are allowed. There is little reason to use this technique with contemporary materials and processes. I worked in a small foundry that did dental metal ingots for the labs. This property of the system is important when suspended solids are present. Most of the references to asbestos for flask or crucible liners were written before this hazard was fully understood. This article will be limited to calcium sulphate-based systems. Poor strength can also generate fins or webs on the casting. Overheating the investment will free sulfur compounds which react with the metal surface and may be very difficult to remove.
Comments
Post a Comment